Since Boarding the Pirate Ship, September Has Become a Time to Reflect on the Years I Spent as a Plumbing Instructor (It was a LABOR of Love!)
Every year at this time, I get a nervous feeling, one I got when I was a high school plumbing instructor and the summer break was over. I always started a countdown 12 days before it officially ended. It was a lot like being on death row for a teacher.
The first day of school for teachers was usually during the last week of August, and in Attleboro, it began with a Convocation; teachers and staff from all the schools in the district gathered in the high school auditorium, where the Superintendent and Assistant Superintendent officially welcomed us back. I always sat with my wife, who has worked for the Attleboro School System for 24 years.
It was a happy/sad day. Despite the excitement of seeing everyone again, we were fully aware that the long haul through a new school year was just beginning.
When I worked at Attleboro High School and flipped on the lights in the plumbing shop for the first time after summer break, I had to smile. The plumbing shop was my home away from home; it was my design, and I built it from scratch with the help of some dedicated adult and student volunteers. For those of us involved, it was a LABOR of love!
The seniors roughed in all the DWV waste and water piping in the mock-up's basement. (Nice Job!)
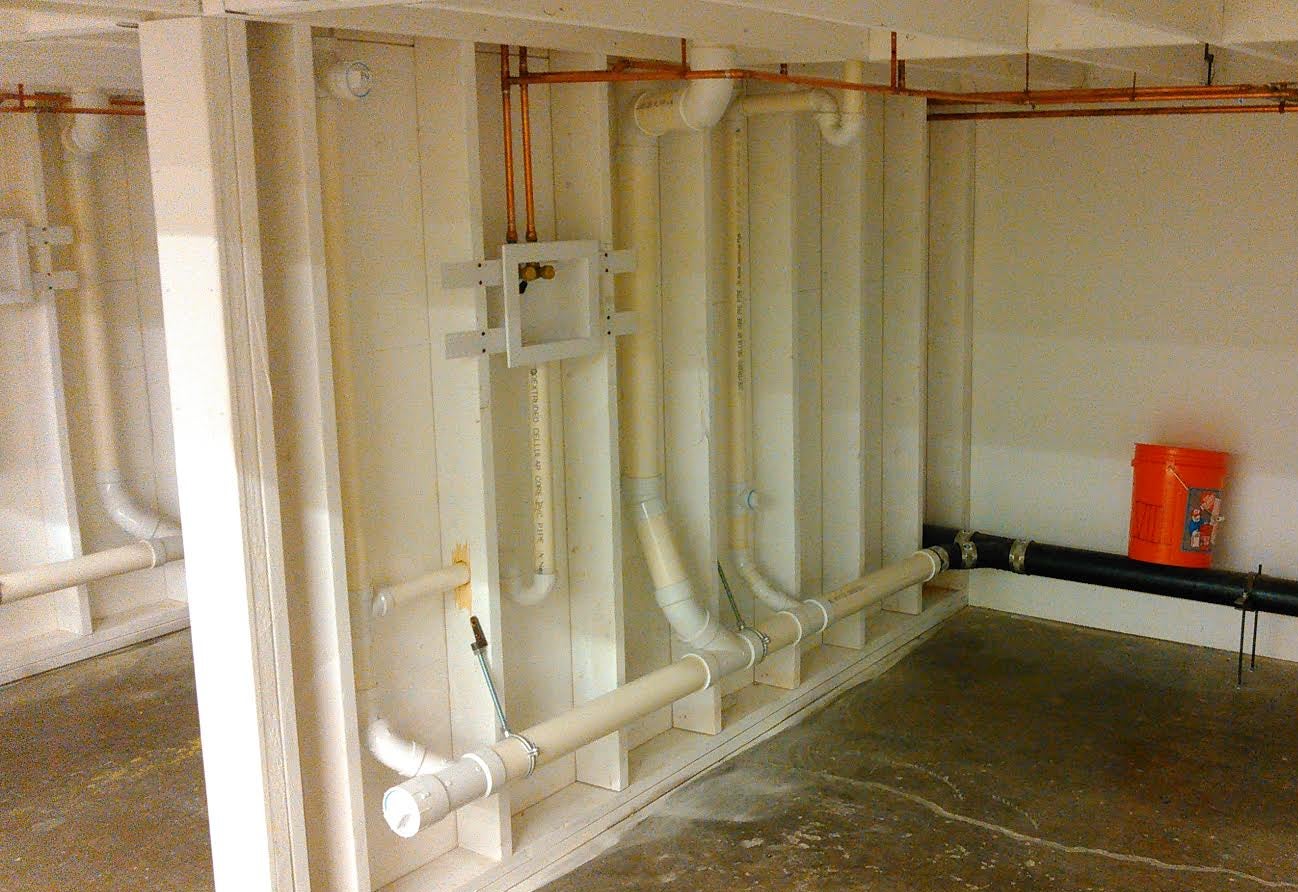
Immediately after I was hired (2013), I offered to come in over the summer to start getting the shop ready, but because the school year hadn't begun, I wasn't an official employee yet, and they wouldn't let me.
The space hadn't functioned as a vocational shop in many years. At one time, it was a machine shop and later a robotics shop. For the ten years before my arrival, it became known as The Graveyard, a place for teachers to discard all their broken chairs, desks, file cabinets, etc., and it was a mess when I toured it during my interview. They promised it would be cleaned out before the start of the school year. It wasn't…
In my first year, because Plumbing was a new program, I only had two classes and a homeroom. There was a freshman exploratory first period and a group of mixed-grade kids who chose plumbing as an elective, sight unseen, second period. In between, I had a homeroom full of seniors.
I was designated a .5, which meant I received half a paycheck for 17 hours of work. On the books, I was done at the end of second period, around 10:00, but when you take on the challenge of starting a new program, building a plumbing shop from scratch, and writing the curriculum, all of which had to be approved by the state, you expect to put in a lot of unpaid hours, and I certainly did. The first year, I rarely headed home before 5:00, and only after I got a call from my wife asking me where I was. A lot of the full-time vocational teachers flew the coop by 2:30.
One of the first things I did was create a pencil sketch of the mock-up apartments I proposed during my job interview, it was a big part of why I was hired. The engineering teacher took my sketch and assigned one of her students the task of turning it into a legitimate set of plans. It came out great, and the construction of the mock-up was supposed to be a project for the carpentry shop, which would be a win-win for both shops.
But, it seemed no one but me was in a hurry to get it started. The new Career and Technical Education (CTE) Director told me the plumbing shop was the most expensive shop in the school to run, and since I couldn't sell sheds like carpentry, bill for oil changes like automotive, or sell food like culinary, there was no way to recoup expenses… I countered, "We're preparing kids for a career in the plumbing trade and making them productive citizens." And I reminded her that state grants made building the shop both doable and affordable.
The former CTE Director had pushed hard for the addition of a plumbing program. Prior to that, any high school students from Attleboro wanting to take plumbing were sent to Tri-County Regional Vocational Technical High School in Franklin, and the cost to the city of Attleboro to send students there for four years far exceeded the cost of building a shop in an unused space and paying one instructor. At the time, Attleboro was sending eight students to Tri-County for plumbing. Unfortunately, the new CTE Director, my new boss, didn't understand the need, and as a result, we butted heads, and she repeatedly tried to have me fired until she unexpectedly announced her retirement three years later…

Advertisement
The carpentry instructor who was supposed to build the plumbing shop had his own curriculum, and building a plumbing shop would've changed everything for him, and he wasn't overly excited to start building it either. Four months into the school year, and other than the things I could do myself, little else was getting done…
The four battery-vented toilets provided students with a great place to learn…
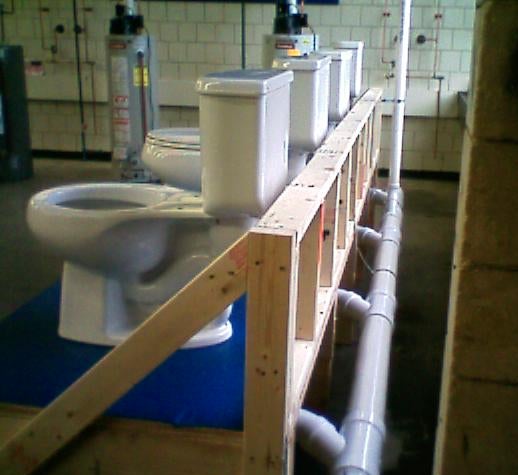
During Blue Pride Night, when parents and residents of Attleboro could tour the school, I met Mike Tyler. Mike was a resident of Attleboro, superintendent of the Highway Dept in the neighboring town of Rehoboth, had a seat on the Attleboro School Committee, and his nephew was one of the seven original students in the plumbing shop.
After Mike formally introduced himself, he asked me what my plans were for the plumbing shop. I showed him my pencil sketch and the engineering plan, and he asked me why the construction hadn't started.
I was upfront with him, telling him the CTE Director thought the shop was too expensive to run and the carpentry instructor who was supposed to build it wasn't in any hurry to abandon his curriculum, which included building sheds he sold to the public.
Mike shook his head in disbelief and assured me he was gonna get involved, and judging by the steely look in his eyes, I knew he meant it.
One late Thursday night, I was in my basement cranking out the miles on my Lemond spinner when my phone lit up. It was an email from Mike to me, the Superintendent, the Assistant Superintendent, the Principal, and the Director of CTE, saying the School Committee had voted to support the building of the plumbing shop and that he would be getting some experienced carpenters willing to volunteer their time to help with the build.
When I ran upstairs and read the email to my wife, she said, "Now they're really gonna hate you for going over their heads…"
The next morning, the CTE Director was waiting for me at the entrance to the CTE wing, and contrary to the reaction I expected, she appeared happy about the good news contained in Mike's email. No one wanted to mess with the School Committee's decision…
One night, I met with Mike and the two carpenters willing to volunteer their time, Don DeVergnes and Tony Lee, and they had a plan that differed from my original sketch. To save time and money, Tony proposed that we balloon frame it. There were nine individual apartments, each having two levels, and he said we could build the partition walls on the ground, stand 'em up, space them appropriately, and attach them to the ceiling and the floor, then add the floor joists in between them for the upper level. The total dimension of the mock-up was roughly 70' long by 14' high by 14' wide. Each individual apartment was 7' wide by 10' deep, and there was a 4' catwalk and a set of stairs with a landing.

Advertisement
Here are two apartments. The 2" x 6" stack walls went up first, and then the floor joists were added. It was faster… The extension of the ledgers were for the 4' catwalk.
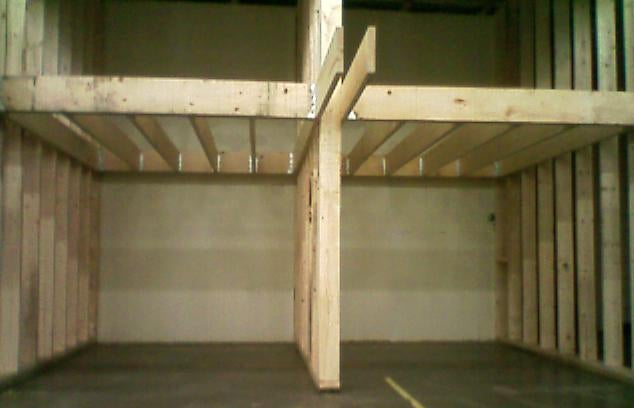
We decided we'd build on Thursday nights from 4:30 to 9:30. We called it Construction Night, and I bought pizza for the crew that varied between seven and ten people, depending on the night. As soon as school ended, I set up the cords and tools so that we could get right to work when everyone arrived. After everyone left, I cleaned, swept the floors, wrapped up cords, and put tools away with Tim Rioux, one of my students who loved working on the shop. I rode/raced bicycles, trained with his Uncle Geno, and was friendly with Tim's stepdad, Geno's brother. Tim and I didn't leave until after 11:00 most nights.
That winter, we got bombarded with over 100" of snow, and the snow days piled up. Despite staging the lumber, a lot of it twisted. Once the floor joists were nailed up, I went in on a Sunday, blocked 'em off, and straightened 'em out. I was working alone, and early in the day, a nail shot out of my nail gun, through the side of a joist, and almost went through my left index finger. I was more embarrassed than hurt, so after I stopped the bleeding, I wrapped it in gauze and continued working.
The blocking helped straighten out the floor joists. Tim and I put up all the plywood after school.
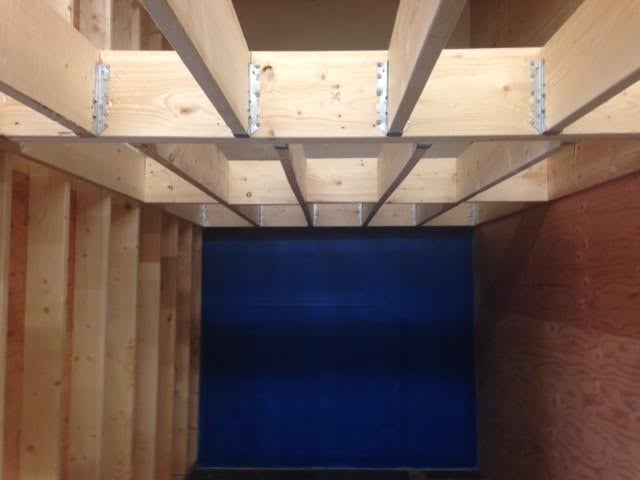
By year two, I was considered a .8, getting paid for 23 hours a week while putting in close to 75 hours to build the shop and write the curriculum, which I usually did from home nights, weekends, and during breaks.
There were a lot of dilemmas along the way, egos that stood in the way of progress, and at one time, everything almost came to a dead halt, but in the end, the mock-up apartments were nothing short of spectacular. When the structure was finished, the electrical instructor sent three seniors over, and they installed lights, outlets, and a panel and wired up an 80-gallon electric water heater donated by Supply New England.
The shop was Chapter 74 Certified by the Department of Elementary and Secondary Education (DESE), and we did it in under two years, a process that normally takes three to five. The inspector from DESE said it was the nicest, cleanest, and most organized shop he had ever seen.

Advertisement
After the mock-up apartments were complete, I built more training stations for the juniors in the middle of the shop.

The last one was a training center for installing tub and shower valves, 16 of them!
In year six of my employment, we were told that a new $260 million dollar state-of-the-art high school would be built with 18 air-conditioned CTE shops. I was probably the only teacher in the building who wasn't happy about knocking down the old building, originally built in 1962, with some parts completed in 1972. I loved my shop just the way it was, but I met with the architects, and together, we designed the new plumbing shop to be very similar to the original.
I left Attleboro High School for Barstool Sports in 2019 before it happened. And it's just as well, I'm not sure I could've handled watching my beautiful shop being demoed.
Here's one of 9 mock-up apartments the seniors finished. Each contained a fully functional three-piece bathroom on the second level.
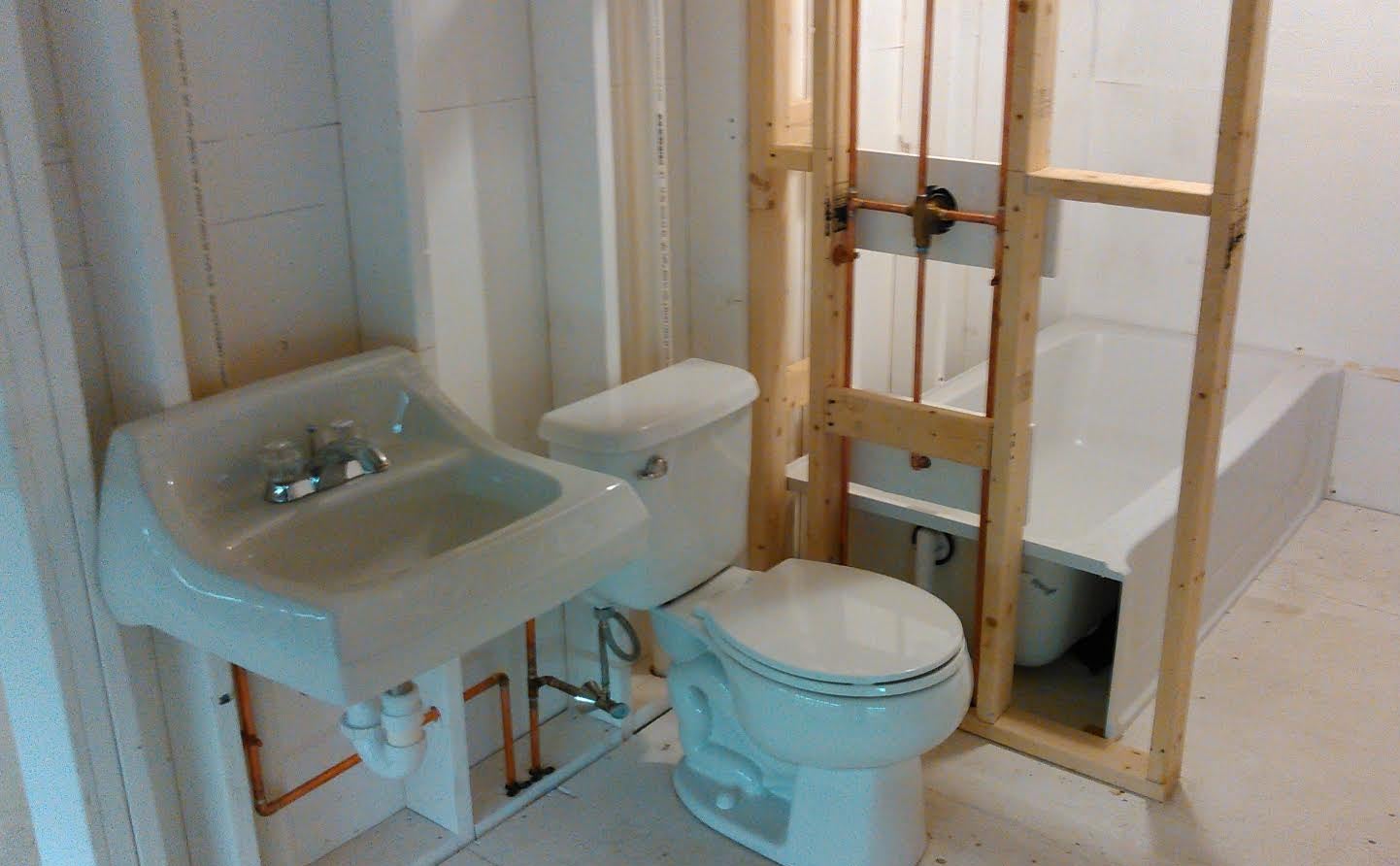

Advertisement
So, this time of year, I reflect on the plumbing program at Attleboro High School, a program I built.
Recently, two of my former students who graduated from Attleboro High School, passed their state exam and became licensed Journeyman Plumbers. Big shout out to Chad Wiegand (Class of 2017) and Jon Marston, Mike Tyler's nephew (Class of 2016). I saw Chad's name in Progress Magazine (PHCC), and Jon texted me his good news.
I could not have been any prouder of these outstanding young men. In addition to being incredible students and damn good plumbers, neither one of them ever missed a Construction Night...
And I'm never going back to my old school…